I’m excited to present our advanced standing seam roll forming machine, tailor-made for manufacturing wall cladding and wall panels. Let me take you through its essential features and operations.
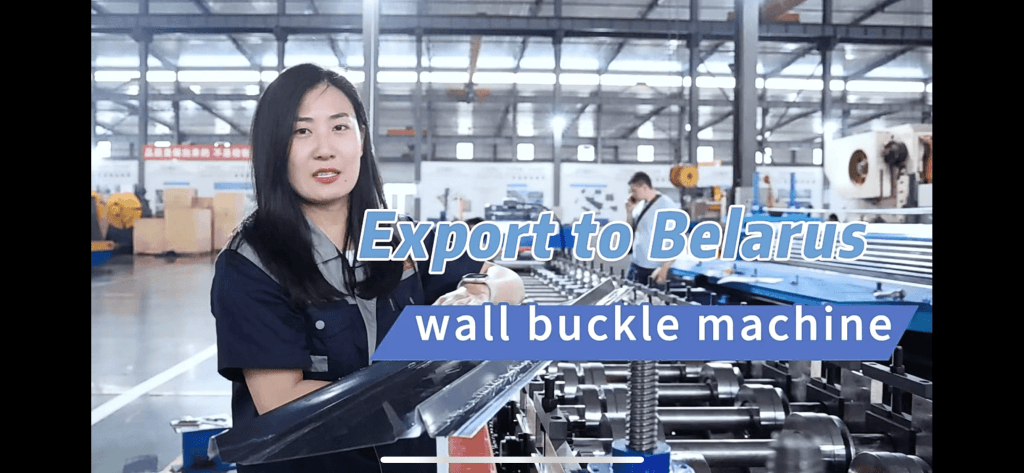
Our three-ton hydraulic decoiler, central to the material feeding, is accompanied by a specialized shaft for film attachment—a unique function that distinguishes our machine from competitors. This film attachment is vital for safeguarding the material’s surface during the rolling process, preventing scratches or damage that could hinder the quality of the final product.
As the material enters the machine, it encounters a set of green rollers. The compact feeding rollers ensure a secure and accurate feeding of the coils into the machine, while the larger active feeding rollers tightly grip the material, facilitating efficient progression through the machine. Additionally, vertical rollers provide guidance, maintaining the material’s direction as it enters the machine.
A notable innovative feature of our machine is the free shearing device, enabling a distinctive sequence of operations: feeding, cutting, and then forming. This order is particularly advantageous for profiles with varying heights and shapes, as it maintains the profile’s design integrity.
In extremely cold regions, like Russia where temperatures can drop to -40℃, we have chosen an electric cutting system over a hydraulic one to ensure uninterrupted operation, as hydraulic oil can freeze in such low temperatures. The electric cutting system is both convenient and dependable, eliminating potential issues during machine operation.
The finished product exemplifies the precision of our machine, with holes punched by specialized rollers that simplify installation and screwing. The product width can be adjusted, providing flexibility to accommodate diverse design needs. This adjust ability is enabled by our PLC control system, ensuring accurate and consistent product dimensions.
Our machine is fitted with three distinct rollers, each playing a specific role in creating the ribs for wall cladding panels. This design allows for the production of panels with various rib configurations, catering to a broad spectrum of aesthetic preferences. The machine’s transmission, controlled by a servo motor, allows for precise adjustments to achieve the desired product width.
With wall cladding panels gaining popularity due to their appealing appearance, our machine is designed to meet the market’s diverse demands. If you’re interested in our machine’s capabilities, please don’t hesitate to reach out with any inquiries. Thank you for your attention, and I’m eager to discuss how our standing seam roll forming machine can elevate your production process.