At the heart of our machines, we employ an efficient and precise double-blades cutter device. The ingenuity of this design lies in its ability to ensure that numerous wave peaks maintain their original shape and structure during the cutting process, avoiding any deformation.
Typically, cutting blades are installed at the material output position after forming. But have you ever noticed that our cutting blade is uniquely positioned inside the machine?
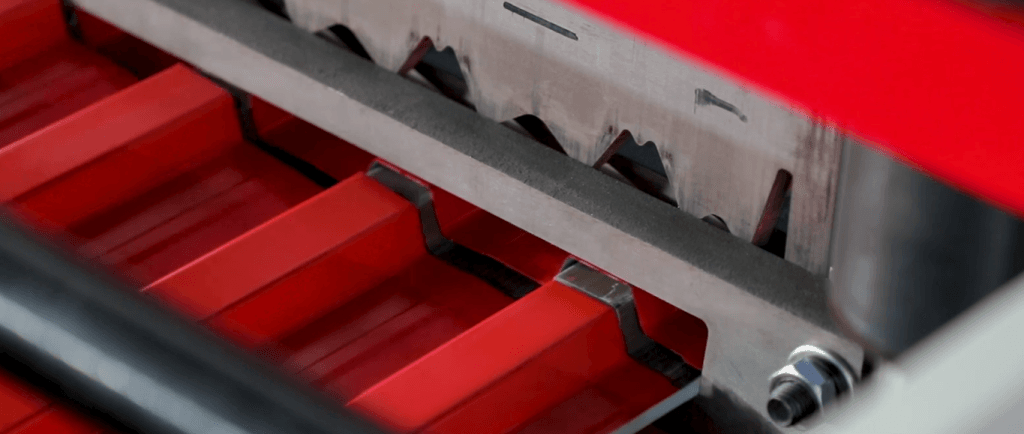
Observe this location and the opposite position, and you will find that both edges are at a 90-degree angle. This design is not coincidental but ensures precise mating of the edges. If the cutting were to occur after mating, the edges might overlap due to the cutting, making subsequent processing cumbersome. Manually lifting the mated parts would not only be inefficient but could also lead to material deformation, affecting aesthetics. Therefore, we choose to use the cutting blade for precise cutting when the edge reaches a 90-degree angle.
The cut material then undergoes further processing through two side rollers and a shaping track to ensure perfection. The resulting material end is precisely positioned within the joint gap, facilitating direct mating without manual intervention.

Upon close inspection, you will find the surface smooth and flawless, with no damage to the paint or embellishments, perfectly preserving the original texture and aesthetics.

In summary, our Australian-style roller shutter door forming machine is not just a simple forming device. It comprehensively considers various problems and challenges that may arise during equipment operation and provides perfect solutions. This is a true 2.0 version of a roller shutter door machine, whose output material can be directly fed into a sewing machine and hemming machine to effortlessly create a beautiful roller shutter door.