The metal embossing machine, also known as a stucco metal embossing or checkered plate making machine, is a specialized piece of equipment designed for imprinting various patterns onto sheet metal surfaces. This machine achieves decorative or functional outcomes by precisely controlling pressure and mold movement to transfer pre-designed patterns or textures onto metal.
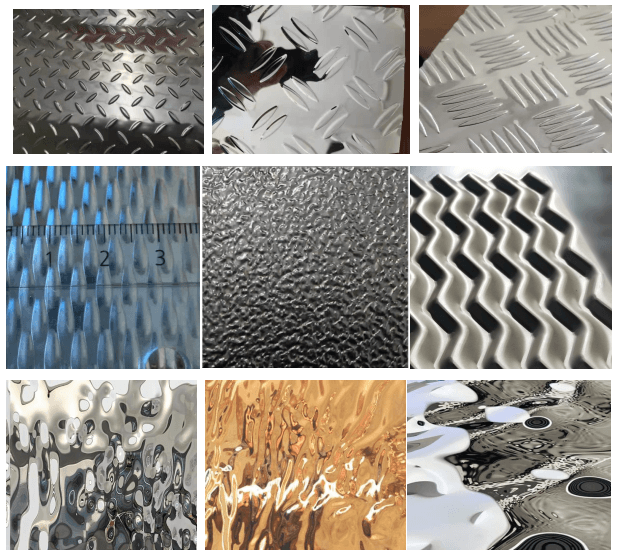
Operating on the principle of physical deformation, the metal embossing machine applies mechanical force to induce plastic deformation on the metal’s surface, creating the desired pattern. Operators start by placing the sheet metal on the machine’s work table and selecting the appropriate embossing mold, typically crafted from tungsten carbide or other robust materials for clear and enduring embossing results.
Versatile in its applications, the sheet metal embossing machine is widely used in metal processing. It’s ideal for creating decorative items for architectural and furniture hardware, as well as manufacturing functional metal parts for high-end industries like automotive and aerospace. In the automotive sector, for instance, it can produce interior parts with distinctive textures, enhancing vehicle aesthetics and comfort.
Overall, the metal plate embossing machine is a precise and efficient tool for metalwork, offering extensive design possibilities through physical deformation. As technology evolves and market demands shift, the capabilities of this machine continue to improve, catering to a wider array of specialized and customized production requirements.
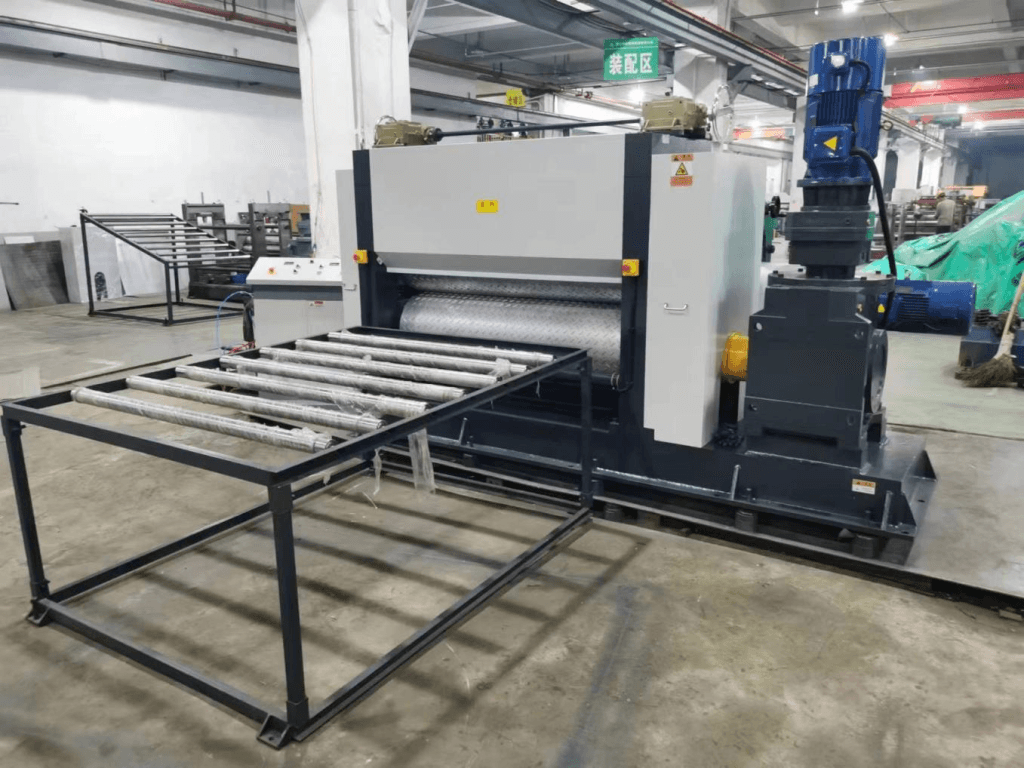
Our Advantages:
1. Embossing rollers are crafted from alloy forged steel, treated with intermediate frequency quenching to achieve a hardness of HRC 55-58.
2. Drive system: Features variable speed control via frequency conversion.
3. Machine frame: Constructed with a solid steel arch frame for superior strength, as opposed to welded square tubing.
4. Interchangeable embossing rollers allow for pattern versatility; we can design and manufacture new rollers or provide design drawings for local processing.
Client-Friendly Operation:
One common query from clients is how to adjust the gap between the rollers. The process is straightforward and can be easily managed using a manual wheel, as illustrated in the accompanying image.
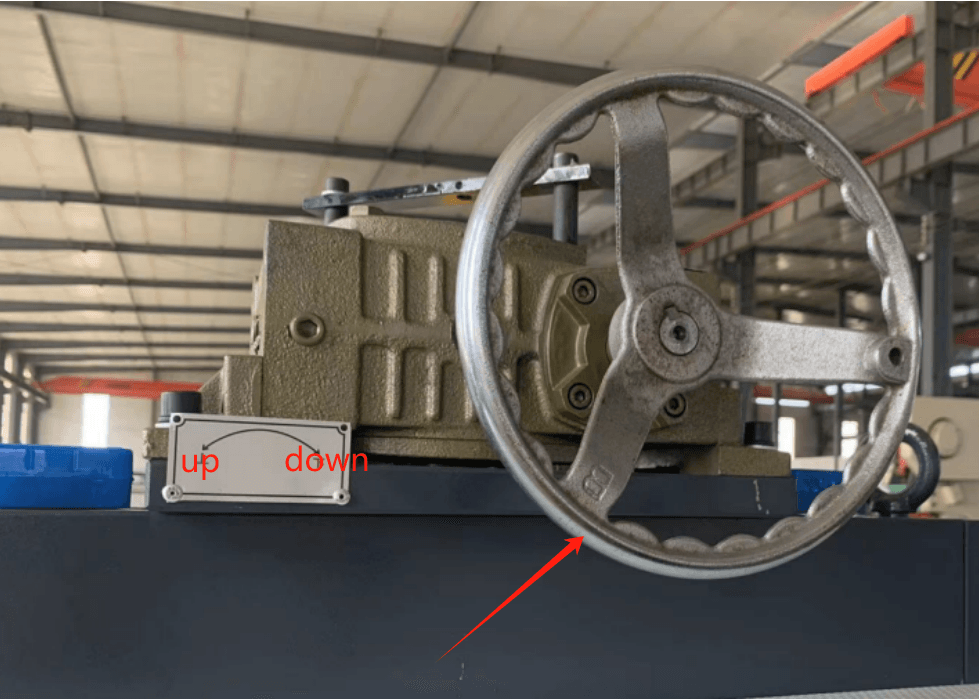